Recognizing the Fundamentals and Applications of Plastic Extrusion in Modern Manufacturing
In the realm of contemporary production, the strategy of plastic extrusion plays a critical role - plastic extrusion. This detailed process, involving the melting and shaping of plastic via specialized dies, is leveraged throughout numerous markets for the creation of varied products. From auto components to durable goods packaging, the applications are substantial, and the capacity for sustainability is just as excellent. Unraveling the basics of this procedure exposes truth flexibility and possibility of plastic extrusion.
The Principles of Plastic Extrusion Refine
While it might show up complicated, the principles of the plastic extrusion procedure are based on fairly straightforward principles. It is a production procedure wherein plastic is thawed and after that shaped right into a constant account through a die. The plastic extrusion procedure is thoroughly utilized in various markets due to its cost-effectiveness, performance, and convenience.
Different Kinds of Plastic Extrusion Methods
Building upon the standard understanding of the plastic extrusion process, it is needed to discover the different strategies associated with this manufacturing technique. Both key methods are profile extrusion and sheet extrusion. In account extrusion, plastic is melted and developed into a constant account, commonly used to produce pipes, poles, rails, and window frameworks. On the other hand, sheet extrusion produces huge, level sheets of plastic, which are usually more processed into products such as food product packaging, shower drapes, and automobile components. Each technique needs specialized equipment and precise control over temperature level and pressure to make certain the plastic keeps its form during cooling. Comprehending these strategies is essential to using plastic extrusion efficiently in modern manufacturing.
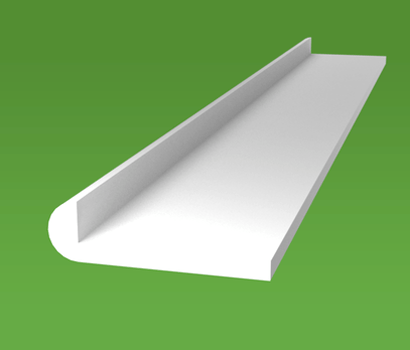
The Role of Plastic Extrusion in the Automotive Industry
An overwhelming majority of components in contemporary lorries are products of the plastic extrusion process. Plastic extrusion is primarily made use of in the manufacturing of various vehicle parts such as bumpers, grills, door panels, and dashboard trim. Therefore, plastic extrusion plays a crucial function in automotive production.
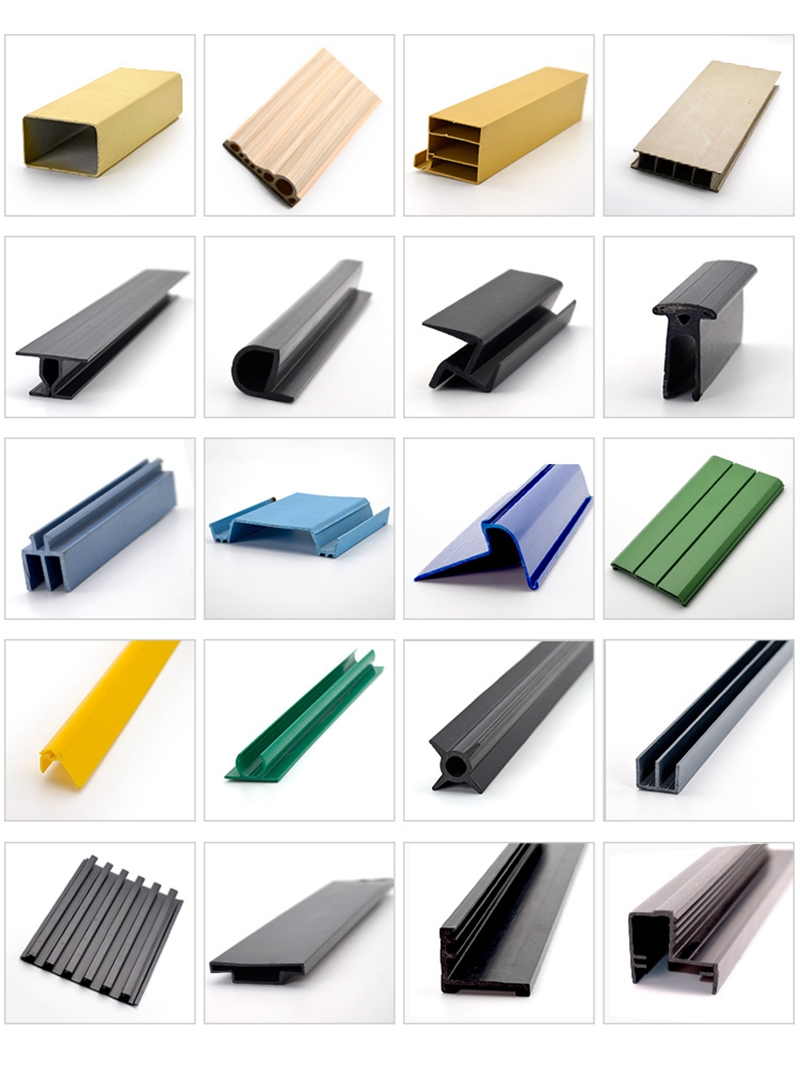
Applications of Plastic Extrusion in Durable Goods Manufacturing
Beyond its significant effect on the auto sector, plastic extrusion confirms equally efficient in the realm of consumer goods producing. This process is vital in producing a wide range of products, from food product packaging to household appliances, toys, and even clinical tools. The adaptability of plastic extrusion enables manufacturers to develop and produce complex shapes and sizes with high accuracy and effectiveness. Additionally, as a result of the recyclability of lots of plastics, squeezed out parts can be recycled, minimizing waste and expense. The versatility, adaptability, and cost-effectiveness of plastic extrusion make it a preferred choice for several customer items producers, contributing significantly to the market's growth and innovation. Nonetheless, the environmental implications of this extensive use call for mindful consideration, a subject to be gone over even more in the succeeding section.
Ecological Influence and Sustainability in Plastic Extrusion
The prevalent use of plastic extrusion in manufacturing invites examination of its environmental effects. As a procedure that frequently uses non-biodegradable materials, the environmental effect can be substantial. Energy usage, waste production, and carbon exhausts are all issues. Nevertheless, market advancements are raising sustainability. Reliable machinery reduces energy use, while waste administration systems reuse scrap plastic, reducing resources demands. Additionally, the development of naturally degradable plastics supplies an extra eco pleasant choice. In spite of these renovations, better technology is needed to mitigate you could check here the ecological impact of plastic extrusion. As culture leans in the direction of sustainability, suppliers should adapt to remain viable, emphasizing the value of constant research and development in this field.
Final thought
Finally, plastic extrusion plays a critical role in modern-day manufacturing, particularly in the automobile and customer goods fields. Its adaptability enables the production of a wide variety of components with high accuracy. Furthermore, its possibility for recycling and growth of naturally degradable materials supplies an appealing method in the direction of this contact form sustainable methods, thereby attending to environmental problems. Comprehending the fundamentals of this procedure is key to maximizing its benefits and applications.
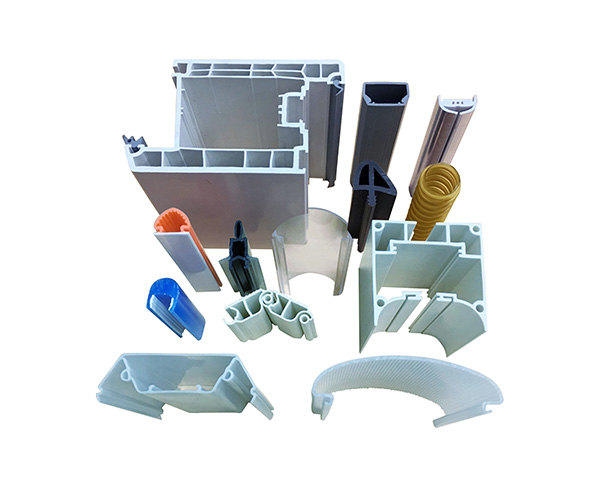
The plastic extrusion procedure is thoroughly made use of in numerous markets due to its cost-effectiveness, convenience, and performance.
Building upon the fundamental understanding of the plastic extrusion procedure, it is necessary to discover the numerous strategies included in this manufacturing technique. plastic extrusion. In comparison, sheet extrusion creates large, flat sheets of plastic, which are usually more processed into items such as food product packaging, shower curtains, and vehicle parts.An overwhelming bulk of special info parts in modern cars are products of the plastic extrusion procedure
Comments on “Plastic extrusion for durable and low-weight components”